
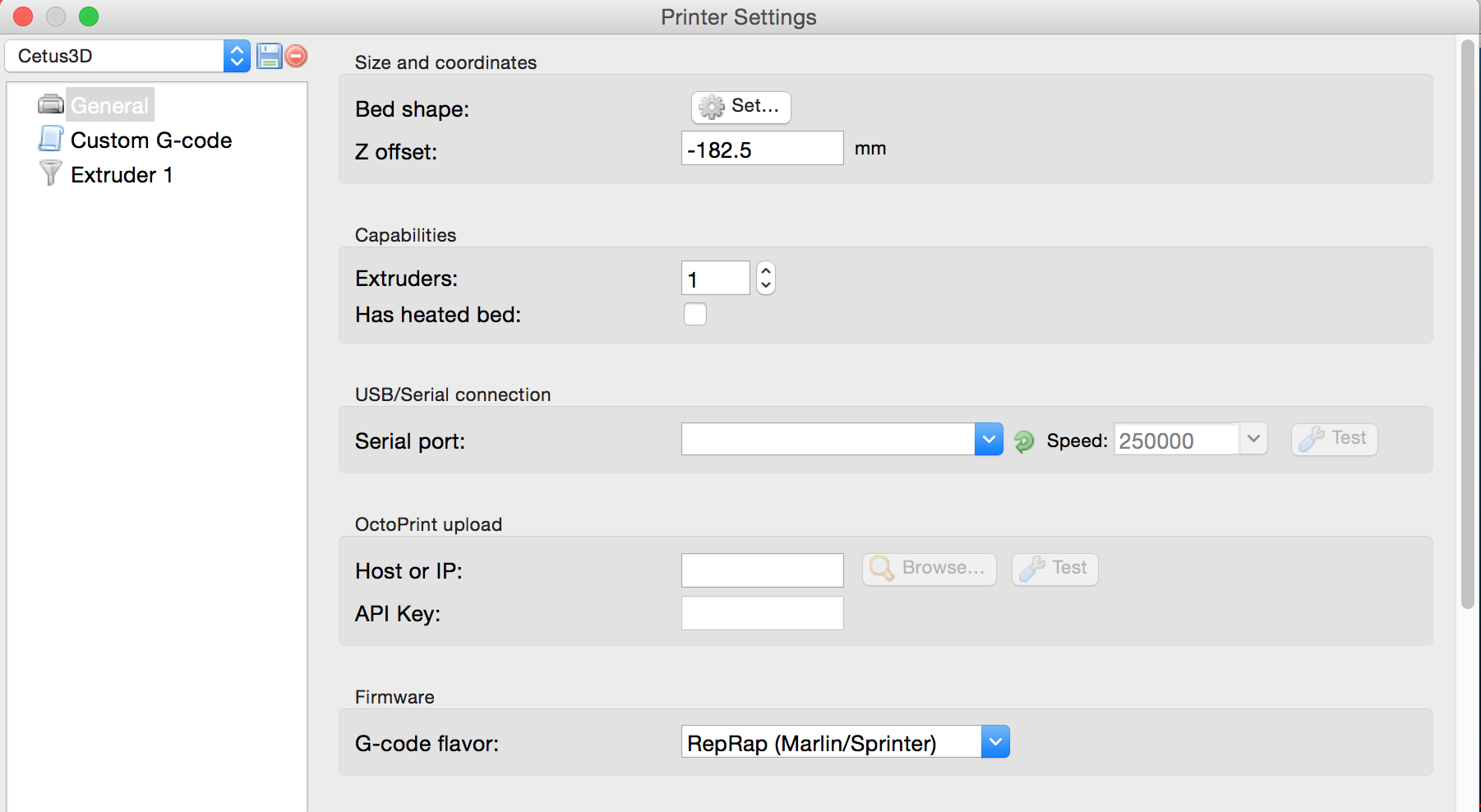
To perform this upgrade, you will need the following hardware:Ĥ80mm (48cm) GT2 Timing Belt, 6mm wide with 2mm pitchġx 16T GT2 bearing idler pulley for 3mm shaftīefore starting this project, go to our thingiverse page and download and print out the printed components associated with this project. (Optional Clip-On Fan Shroud part from our Zero-Offset E3D Adapter) (Optional X-Axis Idler Pulley Alignment Clip) The 3D printable files for this project can be found at the following links:
Cetus3d z banding install#
The X-Axis belt and pulleys will need to be replaced, and you will likely want to install fresh LM6LUU bearings on the new carriage, to obtain a smoother operation than stock, and avoid having to extract the existing bearings from the stock carriage. It is hard to mount the rods perfectly with the couplers, a little misalignment and one introduces wobble (X/Y wiggle).Īnyway, M6 gives slightly higher resolution in Z axis with 0.005mm per motor step.The purpose of this modification is to completely replace the stock Monoprice Select Mini V1/V2 X-Axis Carriage with a 3D printed replacement part, which will serve as a E3Dv6 compatible hot-end mount, but will also feature an integrated belt attachment and tensioning system for a GT2 timing belt. wobble seems mostly introduced by the couplers (either printed or PVC pipe):.less wobble, but still wobble despite of “straight” M6 threaded rods.
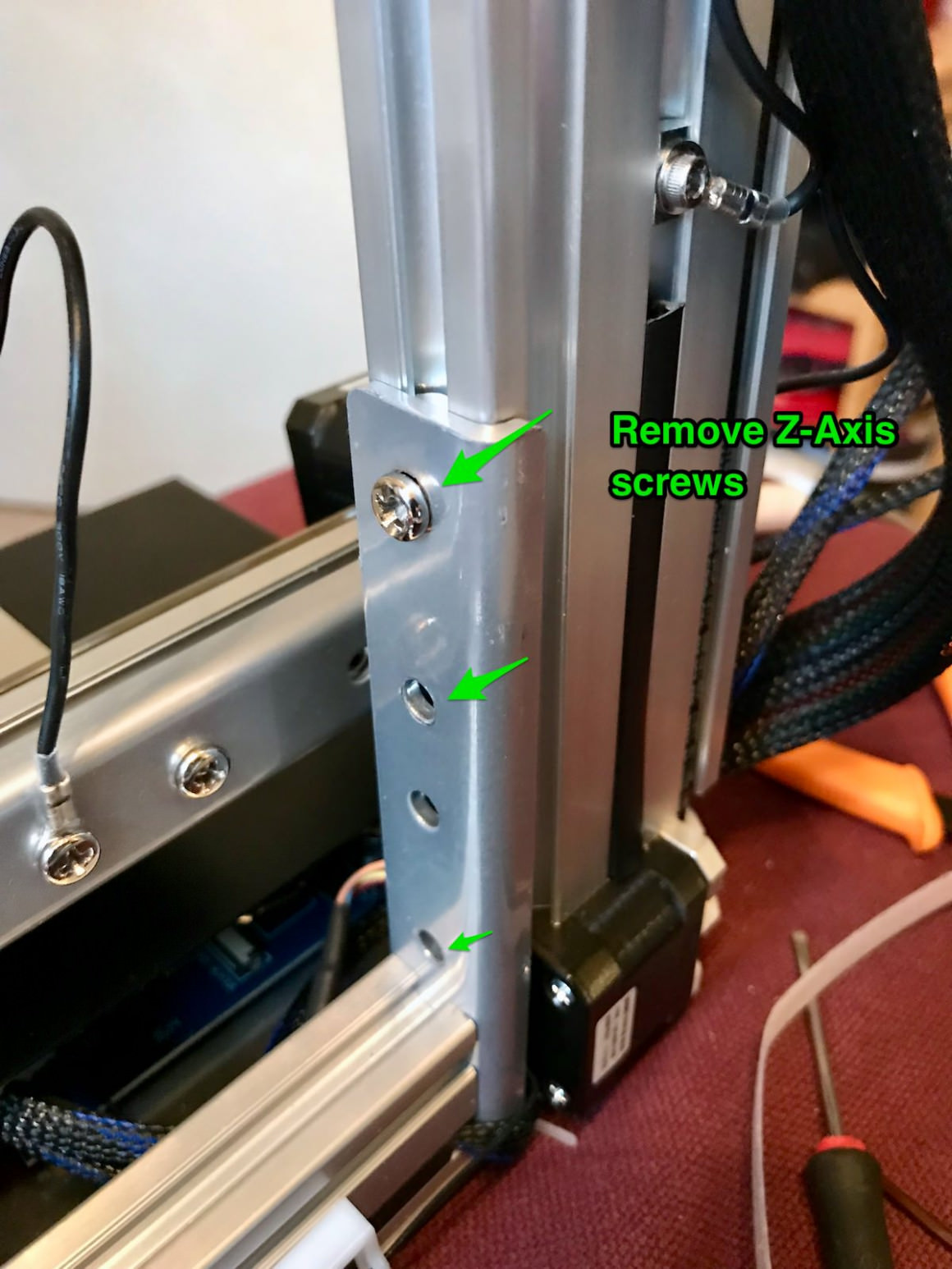
Cetus3d z banding pro#
I made a small package Geeetech / CTC DIY I3 Pro B M6 Z Axis Conversion to use M6 threaded rods instead of M8. Recommendation: print the mounts, print the two bearings, and print the XYZ Calibration Cube or whatever reference item, and see yourself which option works better for you.
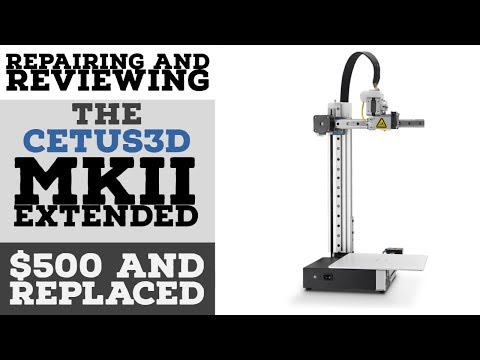

What I noticed was, once I used the printable bearings for a print, and removed it, the threaded rods wobble already less – but as said, best results I achieved with no bearing and wide floating ends or with the tight bearings. whether left and right go the same way or cancel each other wobble out. I would also guess, the unevenness of the threaded rods and their position to each other also matters, e.g. 1-2mm play.īest results I achieved with floating ends or with tight bearing – in other words, either leave it open or make it stay close, but worst is to give it a little play and threaded rods will show their unevenness on the prints. Worst Z wobble was with original Z mount with ~4mm play or the loose bearing with apprx. You may print two bearings (OD 22mm, ID 8mm), make sure to test inner diameter, so the threaded rod slides smoothly – if required use a 8mm drill to widen the inner hole. The new Z bracket provides more space for the threaded M8 rods than the original wooden bracket: The issue isn’t simple: with or without fixation gives good results, some fixation gives more bad print results. Giving it some space on the top means the inherent wobble of the rod is distributed between top and X gantry – giving wobble artifacts on the print. Which means, either give it a lot of space so the upper end of the Z threaded rods can float, and thereby the X gantry can stay fixed (and not wobble) – or – fix the threaded rods and suppress wobble (there is still wobble but restricted).
